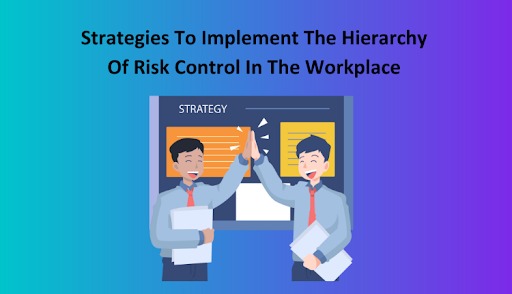
Strategies to Implement the Hierarchy of Risk Control in the Workplace
Organisations across all industries place a high value on employee safety and health. The hierarchy of risk control is a crucial framework for managing and minimising risks in the workplace. Safety experts developed the hierarchy of risk control and have the support of groups like the Institution of Occupational Safety and Health (IOSH). IOSH Courses help us understand the best practices in occupational safety and how an organisation’s Hierarchy of Risk Control in IOSH is essential. This blog will discuss ways to apply the hierarchy of control methods in the workplace to ensure workers’ safety.
Table Of Contents
- Understanding the Hierarchy of Risk Control
- Strategies to Implement the Hierarchy of Risk Control
- Conclusion
Understanding the Hierarchy of Risk Control
The Hierarchy of Risk Control (HRC) is a framework for organising control measures according to their efficacy in lowering risk. In descending order of effectiveness, the five levels make up the hierarchy include:
Elimination
The best control method is to eliminate the danger or the thing that could cause it altogether from the workplace. Redesigning processes, replacing potentially dangerous materials or equipment with safer ones, or automating repetitive tasks are all ways to reduce human exposure to risk.
Substitution
If removing the danger is impossible, replacing it with something less dangerous is the next best thing. Changing out harmful chemicals for safer ones, installing safety features on machinery, or instituting new safety protocols are all examples of what may be required.
Engineering Controls
Engineering controls aim to reduce exposure to risks in the workplace or on equipment. Some examples of measures taken to minimise the risk of musculoskeletal injuries include using ventilation systems to remove airborne contaminants, installing barriers or guards to prevent contact with moving parts, and designing ergonomic workstations.
Administrative Controls
These controls aim to reduce risk by modifying policies, procedures, or work practices. Among these measures could be the introduction of work rotation schedules to lessen the likelihood of repetitive motion injuries, the dissemination of information regarding safe work practices, and the establishment of transparent channels for reporting incidents and risks.
Personal Protective Equipment (PPE)
When all other control measures have been exhausted and proved ineffective, personal protective equipment (PPE) should be reserved as a last resort. Examples include protective eyewear, gloves, headgear, and breathing apparatus. Although personal protective equipment (PPE) can shield workers from some dangers, it is often considered the weakest control measure since it depends on workers to follow instructions and may not deal with the underlying issue causing the risk.
Strategies to Implement the Hierarchy of Risk Control
Conduct a Comprehensive Risk Assessment
Start by conducting a comprehensive risk assessment to identify and evaluate potential risks in the workplace. Collaborate with workers at all levels to catalogue possible dangers, rank the severity of those dangers, and set priorities for control measures according to the risk control hierarchy. Methodically assess risks and choose suitable control measures with the help of risk identification checklists, JHA, and risk matrices.
Prioritise Elimination and Substitution
Eliminating or substituting risks should always precede engineering, administrative, or personal protective equipment (PPE) controls. To eliminate potential dangers, you should find ways to redesign things like processes, equipment, or materials. Look into other options to reduce or eliminate risk without lowering quality or productivity.
Implement Engineering Controls
Put in place engineering controls to ensure that employees are not exposed to risks and to separate them from potential dangers physically. This might include rearranging workstations to eliminate ergonomic risks, adding safety guards to existing machinery, or setting up ventilation systems to filter airborne pollutants. Put into place efficient engineering controls adapted to workplace demands by working with designers, engineers, and equipment manufacturers.
Establish Administrative Controls
To augment engineering controls and strengthen safe work practices, establish administrative controls. Training workers on safe work practices, delivering frequent safety briefings and toolbox talks, and establishing protocols for reporting incidents and risks are all part of developing and communicating clear policies, procedures, and protocols for managing workplace risks. Consistent enforcement and regular evaluation of administrative controls’ effectiveness are of utmost importance.
Conclusion
The management of risks in the workplace and the protection of employees’ health and safety depend on the implementation of the hierarchy of risk control. Organisations can make their workplaces safer and lower the risk of accidents, injuries, and illnesses by following a systematic approach and ranking control measures according to their effectiveness. Organisations can safeguard their most precious asset—their employees—by conducting thorough risk assessments, putting controls in place (both administrative and technical), educating and training employees, and constantly monitoring and improving control measures. Organisations can foster a safe environment where workers are respected, appreciated, and not threatened by risks if they take the initiative to manage risks and strive for safety excellence.